QUALITY RELIABILITY ENGINEERING MANAGEMENT
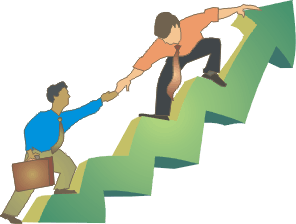
Quality Realiability Engineeirng Management
RELIABILITY
Reliability is defined as the probability that a product, system, or service will perform its intended function adequately for a specified period of time, or will operate in a defined environment without failure.
Stated another way, reliability can be seen as:
Probability of success, Durability, Dependability, Quality over time, Availability to perform a function.
QUALITY VS. RELIABILITY
The difference between quality and reliability is that quality shows how well an object performs its proper function, while reliability shows how well this object maintains its original level of quality over time, through various conditions.
For example, a quality vehicle that is safe, fuel efficient, and easy to operate may be considered high quality. If this car continues to meet this criterion for several years, and performs well and remains safe even when driven in inclement weather, it may be considered reliable.
DESIGN OF EXPERIMENTS (DOE)
Design of experiments (DOE) is defined as a branch of applied statistics that deals with planning, conducting, analyzing, and interpreting controlled tests to evaluate the factors that control the value of a parameter or group of parameters. DOE is a powerful data collection and analysis tool that can be used in a variety of experimental situations.
It allows for multiple input factors to be manipulated, determining their effect on a desired output (response). By manipulating multiple inputs at the same time, DOE can identify important interactions that may be missed when experimenting with one factor at a time. All possible combinations can be investigated (full factorial) or only a portion of the possible combinations (fractional factorial).
Taguchi Method of Quality Control
The Taguchi method, also referred to as robust design method or off-line quality control, refers to a quality product design or engineering technique comprised of statistical control methods usd to inform design, paramaters, and tolerances.
The Taguchi method applied statistical methods to decrease the variability of a product. There are two basic ideas that you can use to describe this methodology:
When measuring the quality, a specified target value deviation should be used.
To ensure quality, product qualities should be built in through appropriate design, and not through inspection and rework.
The Taguchi methods were developed by Japanese research, Dr. Genichi Taguchi. The Taguchi method was incorporated by several companies both in Japan and in the United States. Some of the companies with big names that embraced the Taguchi method include the following:
1.Boeing
2.Ford
3.Toyota
4.Xerox
It was first developed to help improve the the quality of goods manufacturing. However, it was later extended to biotechnology, engineering, advertising as well as marketing. System design – In this phase, engineer designers apply their practical skills together with scientific and engineering methods to come up with a viable, functional design. The system, in this case, may be the creation of anew product or an improvement or modification to an existing design.
Parameter design – In this phase, the designer determines the optimal settings or parameters for the product or process. This allows allows for minimizing the cost of manufacturing and performance variation.
Tolerance design – Tolerance design means tightening tolerances for a product or a process so that quality and performance/productivity are enhanced. Generally, there are limited Taguchi experimental designs which have made it easy for them to choose and use in the environment in which they manufacture their products
Proprietory Software tools for Quality Reliability Engineering Management:
ALD's Software Suite
ALD’s Software Suite consists of a set of integrated tools covering Reliability prediction, Availability, Maintainability Analysis, Safety Assessment, Quality Management, Safety Management, Industrial Process Control, Logistics Support and more:
RAM Commander is the pioneering Reliability and Safety software for reliability professionals and design engineers. List of RAM Commander modules contains Reliability, Maintainability, RBD, Fault Tree Analysis, Event Tree Analysis, Safety Assessment, Spare Parts Optimization/Provisioning, Derating, FMECA and Testability Analysis, Process & Design FMEA and more.
FRACAS a web based and user configurable Failure Reporting, Analysis and Corrective Action System (FRACAS) that captures information about equipment or the processes throughout its life cycle, from design,production testing, and customers support.
Life Cycle Cost (LCC) analysis and Total Cost of Ownership evaluation are the basis for decision making for the wide range of industries and equipment: from IT systems to submarines. LCC analyzes the total ownership costs of various design alternatives and system’s components over the projected life cycle of a system.
SPC (Statistical Process Control) is software for real-time monitoring of the manufacturing process and its improvement.
ReliaSoft
ReliaSoft (Reliability Analysis and Management)
ReliaSoft software provides a powerful range of reliability software solutions to facilitate a comprehensive set of reliability engineering modeling and analysis techniques. We are the leading reliability solution provider for product test, design, maintenance strategy and optimization.
ReliaSoft products support a wide range of reliability and maintainability analysis techniques, such as life data analysis, accelerated life testing, system modelling and RAM analysis, reliability growth, FRACAS, FMEA and RCM analysis to meet and improve reliability of your products, processes and optimize maintenance planning.
Discover how you can achieve success and meet your reliability goals with ReliaSoft software
Life data analysis
Accelerated life testing
Reliability growth
System modeling and RAM analysis
Reliability centered maintenance (RCM)
Failure mode and effects analysis (FMEA)