Plant Maintenance
Plant Maintenance
Plant maintenance is the service and repair of assets and equipment. During normal operation, assets may accumulate wear-and-tear that needs to be addressed. Deviations outside of normal operation of cause the majority of damage to equipment and assets.
Plant maintenance includes scheduled and unscheduled maintenance. Plant maintenance may be scheduled according to age of equipment or usage of equipment. Unscheduled plant maintenance can occur after equipment failure or operation excursions.
Plant maintenance can cause downtime due to process disruption and critical assets being taken offline for servicing. During plant maintenance, input supply chains may lose efficiency as assets are unable to process at their normal rate. The short-term reduction in profitability caused by process disruption, as well as the costs associated with servicing or repairs, often leads many companies to defer plant maintenance.
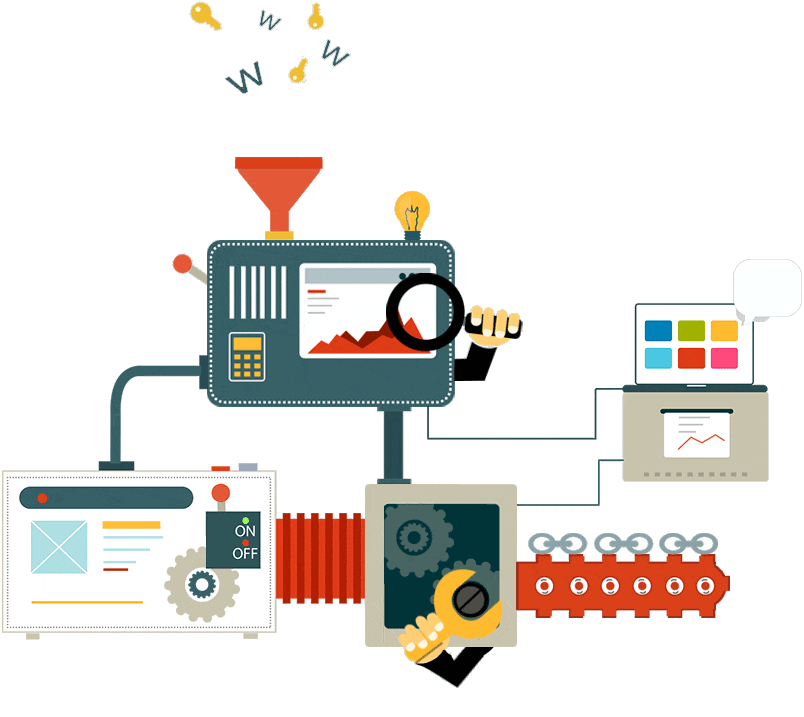
Predictive maintenance uses sensor data to predict when to schedule plant maintenance. Comparing current sensor data against historical data can point toward conditions that lead to. Traditionally, this data has been integrated by human operators who use rules-of-thumb and intuition to link sensor data to required plant maintenance. Plant operations staff may lack the time and attention needed to detect signs that plant maintenance is required, leading to over- or under-prescribed plant maintenance.
More recently, machine learning and artificial intelligence (AI) have been applied to the problem of plant maintenance. By comparing historical sensor data with asset failure, software can detect failure signatures long before human operators would notice anything outside of normal operation. The Aspen Mtell® software can notify plant operators months prior to the failure of a valve, seal, heat exchanger or other piece of equipment.
Being able to intelligently schedule downtime gives plant operators more control over plant maintenance. Multiple pieces of equipment can be serviced simultaneously, and supply chain logistics can be adjusted to reduced asset throughput.

Mechanical Maintenance
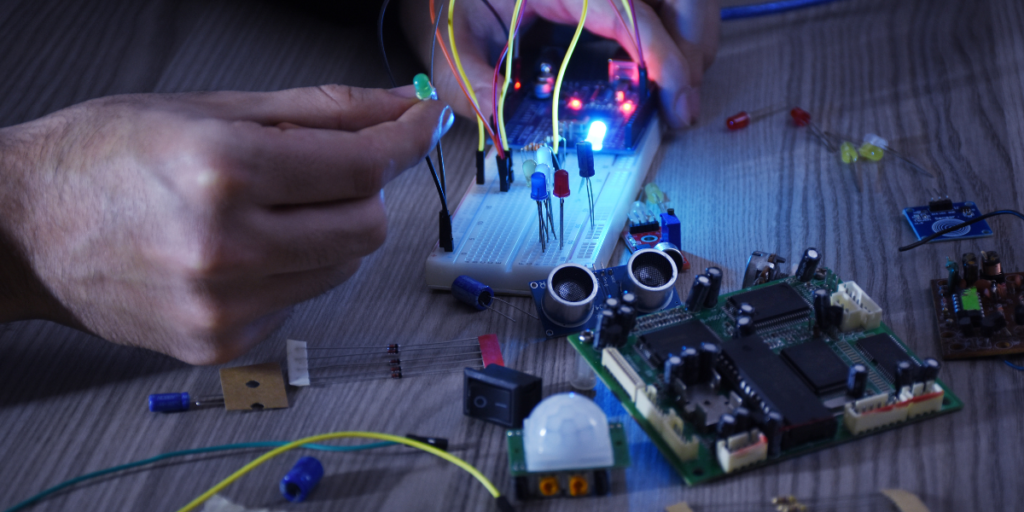
Electrical Maintenance
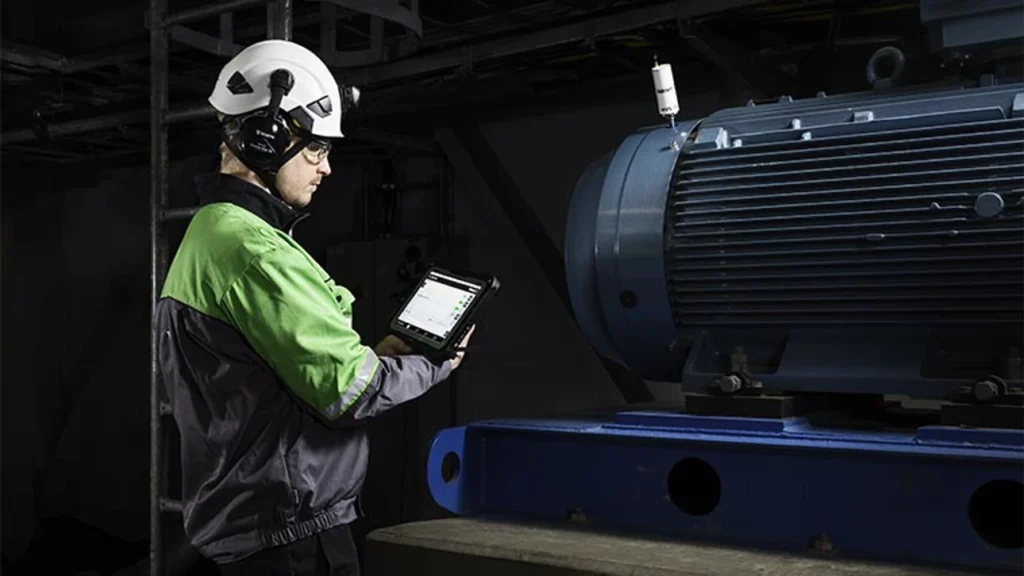
Instrument Maintenance
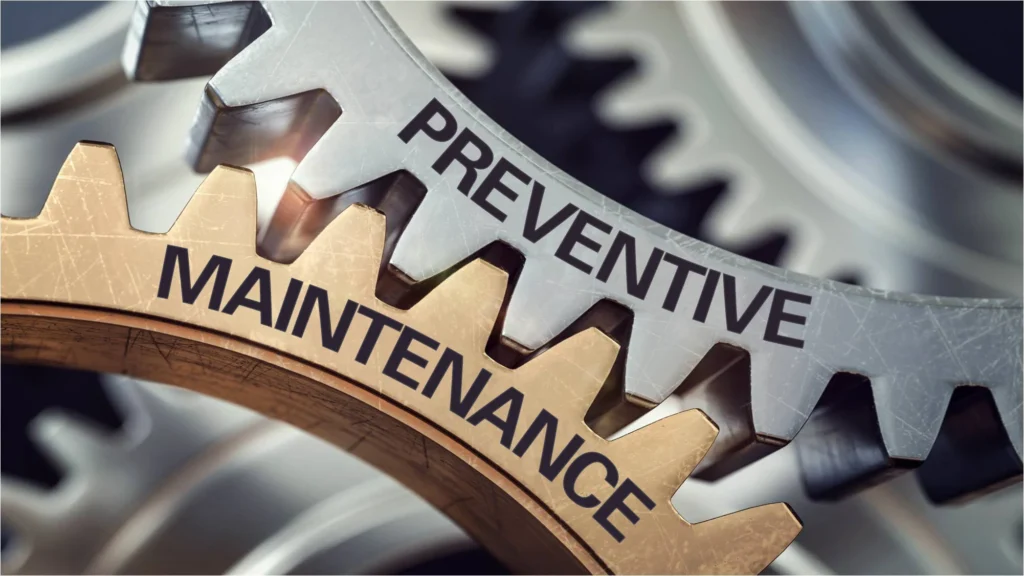
Preventive Maintenance
Your trusted partner in optimizing equipment performance and ensuring longevity through comprehensive Preventive Maintenance (PM) solutions. In today’s fast-paced and competitive business landscape, the importance of preventive maintenance cannot be overstated.

Reliability Centred Maintenance
Where operational excellence meets cutting-edge Reliability-Centered Maintenance (RCM) solutions. In the dynamic landscape of modern industries, ensuring the reliability and performance of critical assets is paramount. Our RCM services are designed to empower businesses by strategically optimizing maintenance efforts, minimizing risks.
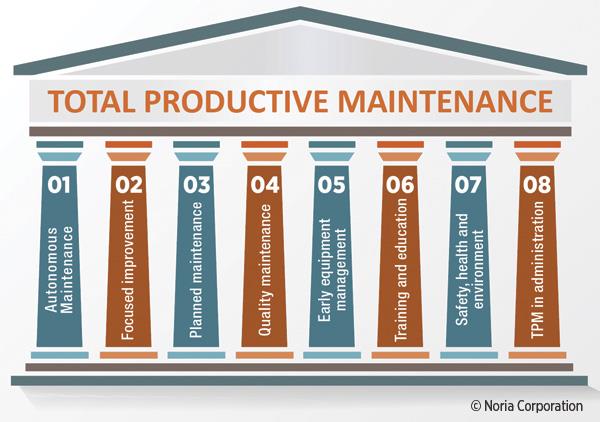
Total Productive Maintenance
In today’s competitive business environment, maximizing the efficiency and effectiveness of your production processes is essential for success. Our TPM solutions are designed to optimize equipment reliability, minimize downtime, and empower your organization to reach new heights of productivity.

Lean Maintenance
In an era where efficiency is paramount, our Lean Maintenance solutions are designed to optimize your maintenance processes, eliminate waste, and ensure that your operations run seamlessly. Explore how our Lean Maintenance approach can revolutionize your maintenance practices and contribute to the overall success of your business.