Vibration Analysis In Kalpakkam
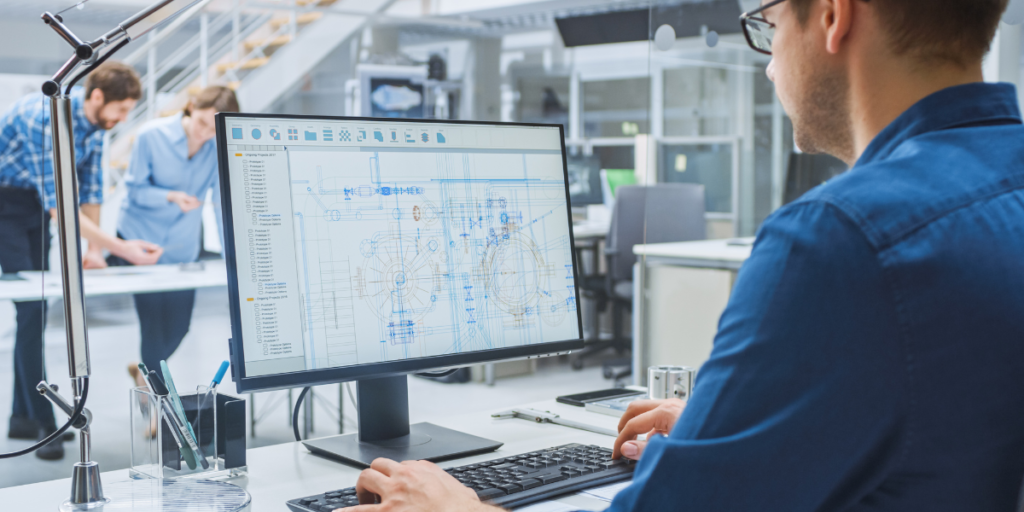
Vibration Analysis In Kalpakkam is a crucial technique used in the maintenance of industrial machinery to assess its condition and detect potential faults. By analyzing vibrations produced by equipment during operation, engineers can identify issues such as misalignment, imbalance, bearing defects, and structural weaknesses. This blog delves into the principles of vibration analysis, its applications, benefits, and how it helps in maintaining optimal performance and reliability of machinery.
Principles of Vibration Analysis
Vibration analysis relies on the principle that every machine generates a unique vibration signature during operation. This signature changes with the machine’s condition, making it possible to detect abnormalities before they lead to serious malfunctions.
Applications of Vibration Analysis
Early Fault Detection: By monitoring vibration patterns, maintenance personnel can identify early signs of mechanical issues, allowing for timely repairs and preventing unexpected breakdowns.
Condition Monitoring: Continuous vibration analysis provides insights into the overall health of equipment, helping to plan maintenance activities proactively based on actual machine condition rather than scheduled intervals.
Root Cause Analysis: Vibration data helps in determining the root causes of problems such as misalignment, worn-out bearings, resonance, and structural weaknesses, enabling targeted corrective actions.
Benefits of Vibration Analysis
Reduced Downtime: Early detection of faults minimizes unplanned downtime, ensuring that production schedules remain on track.
Cost Savings: Preventive maintenance based on vibration analysis is more cost-effective than reactive repairs, as it prevents costly failures and extends the lifespan of equipment.
Improved Safety: Regular vibration analysis enhances equipment reliability and safety, reducing the risk of accidents caused by malfunctioning machinery.
Enhanced Efficiency: Well-maintained machinery operates more efficiently, consuming less energy and optimizing overall productivity.
Techniques and Tools Used in Vibration Analysis
Accelerometers: These sensors measure acceleration and convert it into electrical signals, providing data on vibration levels.
Vibration Analyzers: Portable devices that analyze vibration signals, displaying frequency spectra and identifying anomalies.
FFT (Fast Fourier Transform): A mathematical technique used to convert time-domain vibration signals into frequency-domain spectra for detailed analysis.
Software Solutions: Advanced software programs process vibration data, perform trend analysis, and generate maintenance recommendations.
Implementing Vibration Analysis Program
Baseline Measurement: Establish initial vibration signatures for equipment under normal operating conditions.
Regular Monitoring: Schedule periodic vibration measurements to monitor changes in equipment condition over time.
Data Analysis and Interpretation: Analyze vibration data to identify trends, anomalies, and potential issues requiring attention.
Actionable Insights: Use analysis results to plan and prioritize maintenance activities, ensuring effective resource allocation.
Case Studies and Real-World Examples
Manufacturing Industry: A case study showcasing how vibration analysis helped a manufacturing plant reduce downtime by 30% through proactive maintenance.
Energy Sector: An example of how vibration analysis prevented catastrophic failures in turbines, saving millions in repair costs.